Menu
- Repairs
- Jeep CJ Upgrades
- Rear Tire Carrier
- Suspension Lift
- Transfer Case Lowering Kit
- Edelbrock Upgrades
- Body Lift
- Beard Seats
- Axle Upgrades
- Locking Hubs
- Stud Conversion
- Rocker Panels
- Gas Tank Skid
- On Board Air
- Rubicon Express Lift
- Sway Bar Disconnect
- D-Ring Mounts
- Roll Cage
- Dual Battery Wiring
- Dual Batteries
- Spring Over Lift
- Wheels
- Speedo Gear
- Jamboree Rack
- CB Antenna Mount
- Fuel Pressure Regulator
- Throttle Body Injection
- Multi Port Injection
- Howell TBI Installation
- MobiWeld Alternator Install
- Install TJ Flares on a CJ
- Quarter Elliptic Install
- EZ Locker Install
- Herculiner
- CJ 4.0 Engine Swap
Throttle Body Injection
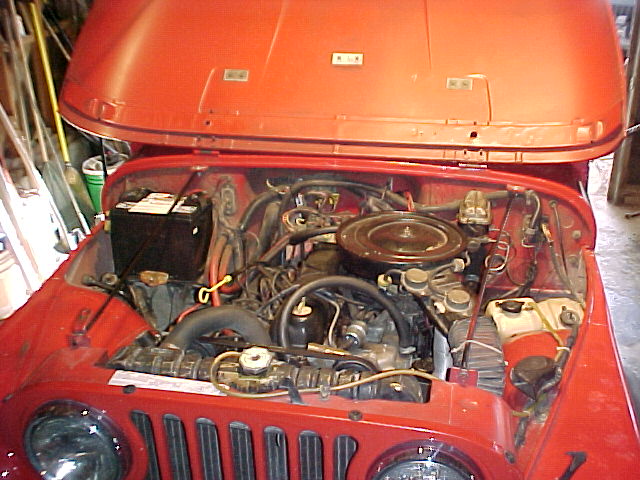
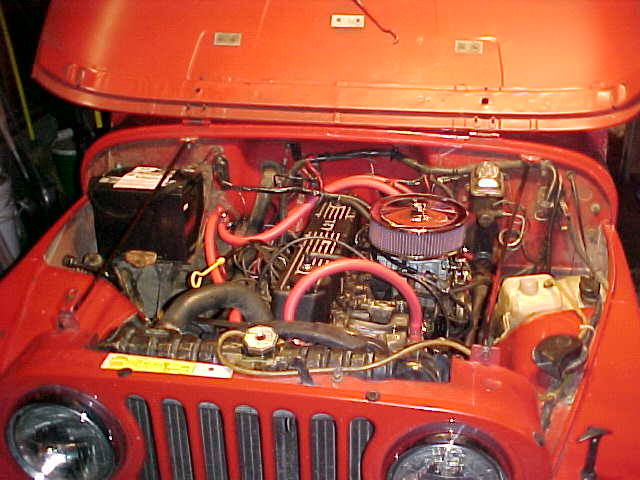
HOWELL THROTTLE BODY INJECTION
This project is another solution for your stock Carter BBD carburetor and all its inherent problems. Right away, you'll notice this isn't my CJ in these photos. This Jeep also goes into the "research" of Jeeps for this site. This is a 1985 CJ-7 with a similar 258 inline six motor. On this Jeep, the owner had more of a "budget" in mind, yet still had the Carter BBD that didn't want to pass smog or maintain an idle. The Howell TBI injection was ordered to solve the problem. Follow along as we install this also-popular conversion for the Jeep motor.
What Is It?
The Howell TBI kit is the least-expensive of the two California-legal fuel injection conversions for the Jeep. Howell is the man who designed the fuel injection systems for General Motors. Not too surprisingly, this kit is based from a TBI system from a GM 4.3 liter V-6 motor.
The biggest difference between the Multi-Port Injection (MPI) and the Throttle Body Injection (TBI) systems is the way the fuel gets inserted into the cylinders. The TBI system uses the existing conventional intake manifold by replacing the carburetor with an electronically-controlled injection system. Once the fuel is injected into the intake, it must travel through the various intake funnels to each of the cylinders. The middle two being the closest to the injector and the outer two being the furthest. Thus, the system is not much different than a typical carburetor in terms of its fuel delivery. A multi-port injection system, in contrast, has a separate injector at each cylinder, so each cylinder gets a metered (equal) amount of fuel.
Both systems solve the Carter BBD problems of poor idle (stalling) and troublesome vacuum lines! Both systems are an absolute improvement over the stock carbureted system. Both systems will cost you some money to convert your engine. And both system will produce results. What are you waiting for?
Before You Order A Kit!
Unlike the Mopar conversion project, the Howell conversion DOES rely on some of the stock emissions functions such as the Exhaust Gas Recirculation (EGR) valve, the Evaporation Canister, and the Coolant Temperature Override (CTO) valve, as well as some stock electrical components like the Ignition Module. If these items are faulty before the project, the conversion is going to have the same stalling characteristics when you are finished! Beware.
The Howell conversion did not require as many specialized tools as the Mopar conversion. Pretty much all of the job was done with common hand tools. You will need a small tubing cutter and a flairing tool for the fuel line, and it helps to have a good wiring tool, a wire tester, and an Ohm meter.
This project is fairly straight-forward. The wiring part was intimidating as the instructions seemed a little confusing at first, but became rather obvious once things got going.
Getting Started!
This kit was Model JP-1 and covers the Jeep 258 CID (4.2 liter) 6 cylinder engines from 1972-1991. These steps will generally follow the instructions included in the kit. However, the instructions were based on a 1990 Jeep Wrangler and there were many instances in the instructions where the wire colors or locations were not the same as indicated in the instructions. Hopefully, this project page will provide another example/detail of the conversion process.
ORGANIZATION | |
![]() |
Step O-1 When you open the kit, find the sealed white envelope that contains the instructions and other documentation. On Page 1 of the instructions there is a list of Kit Components (including part numbers). Go through the parts and check everything is there. We found some of the parts listed actually had different part numbers than what was listed in the Kit Components. Turns out there are a few new part numbers since the instructions were printed. |
![]() |
Step O-2 Read through the instructions. The Howell kit features a nice service manual that will be handy later on when trouble-shooting problems. Also, the photos in the instructions were pretty clear. The folks at Mopar should take note of this one, it was a real plus! |
DISASSEMBLY |
|
Step D-1 | As with most projects under the hood, it is always recommended that you disconnect the ground cable from the battery to avoid inadvertently shorting out an electrical component somewhere else. |
![]() |
Step D-2 Remove the mechanical fuel pump. Since the fuel injection system requires the use of an electrical fuel pump, this opening will need to be covered. A block-off plate is included in the kit, along with a gasket. The block-off plate can be installed at this time. |
![]() |
Step D-3 Remove the air filter tray. The tray includes the Thermostatic Air Cleaner System (THERMAC) which will no longer be needed. Toss them in a box. |
![]() |
Step D-4 Starting at the carburetor, remove the fuel filter, fuel-in line (that came from the old fuel pump), and the fuel-out vapor line (down to the driver's side frame rail). Then remove the throttle return spring(s), the electric choke heater wire, the WOT switch connector, the Stepper motor plug, carburetor bowl vent line (which goes to the charcoal canister, and needs to be plugged at the canister - see photo), idle solenoid vacuum line, and the vacuum line to the vacuum switches on the back of the valve cover. Disconnect the linkage arm, the PVC/canister vacuum line, and the vacuum line that runs to the distributor advance, all of these parts will be reused (replace hoses if necessary). |
![]() |
Step D-5 Disassemble and remove Upstream and Downstream check valves and pulse air system. This will probably require you to cut the air tube from the catalytic converter and the exhaust header pipe. Don't forget that later these ends will need to be sealed! Attached to the parts associated with the Pulse Air system is the Decel valve (including its bracket) and that needs to be removed, too. |
Step D-6 | The remaining vacuum lines can be removed at this time. These include the 4" (beige) & 10" (green) Hg vacuum switches (mounted on the fire wall above the rear valve cover), the PCV solenoid, and the vacuum reservoir (small "tin can" located below the battery). Also, the Knock sensor (red swivel cap on intake manifold) can be removed. Pop the cap off and unthread the sensor from the manifold. Any odd brackets left over from parts removed can also be removed. |
![]() |
Step D-7 Now the carburetor can be removed from the
intake manifold. While you're at it, the four studs that hold the carburetor down
also need to be removed from the intake manifold. Use two of the old nuts that held
the carburetor down and tighten them together on one stud, then extract the stud by
"loosening" the lower-most nut. Once the studs are off, clean the mounting surface and remove any stubborn gasket material that may be stuck on the surface. |
![]() |
Tip! When removing any of the wiring from parts that will still be used, make sure to label the wires. This will help you recall where everything needs to go later. |
![]() |
Step D-8 Since this CJ does not have power brakes, the old manifold port (below the carburetor) vacuum source was no longer needed. A brass plug was purchased and inserted to cleanly seal off the opening. (You can see the old fitting on the second photo in Step D-7 above.) |
![]() |
Step D-9 With the intake manifold slightly more "exposed" the Coolant Temperature sensor can be removed. The old one is shown here on the left next to the new unit. Keep in mind, when you pull this out you will have a mess on your hands unless you drain (or partially drain) the coolant from your radiator. |
![]() |
Step D-10 As long as you're in the neighborhood, you can pull the O2 sensor from the exhaust header pipe as well. I recommend NOT INSTALLING the new O2 sensor just yet. It is better to keep it safely tucked away in the box until you are ready to install the new wiring harness. |
Detour | Since we had most of the top of the motor exposed at this point, we took this opportunity to swap out the leaky plastic valve cover on the CJ. We installed a new aluminum valve cover and it really added a nice touch to the new Howell TBI unit under the hood! |
WIRING This next series of steps will continue with the final steps of the Disassembly process and will merge into the beginning of the Assembly process. |
|
![]() |
Step W-1 Remove the glove box insert, and disconnect the old ECM main wiring plug. Remove the ECM from its bracket by removing the one retainer screw from the bottom forward edge as it faces you. You will note that the new ECM (left) is slightly longer than the old one (right). |
Step W-2 | Remove the rubber bracket on the firewall (from the engine bay side) and pull the remaining wiring harness and the ECM plug out through the large elongated hole in the wall. You will want to reuse this rubber bracket (see Step W-9), so cutting it from the side will be the easiest. To make matters more fun, you'll discover there is metal inside this rubber bracket. Be careful! |
![]() |
Step W-3 The instructions require you to find two wires within this wiring harness. If you remove the outer sheath of the harness (tape and plastic) you'll note there is a twisted pair of wires (orange and purple). These are the two wires you are looking for, and they connect with the distributor. Extract these twisted pair from the harness by cutting them and carefully pulling them out. |
Step W-4 | The Jeep is equipped with a duraspark ignition module (mounted on the front driver's side fender well, below the windshield washer and coolant over-flow bottles. This module has two plugs attached to it. One plug has four wires, and this plug attaches to wires from the old wiring harness starting from the old ECM. The other plug has only two wires, and this plug attaches to wires from the MAIN wiring harness that attaches to the firewall at the main fuse block (driver's side). It is the four-wire plug that we are focusing on! |
![]() |
Step W-5 You will note that the four-wire plug
attaches to a three-wire plug from the old harness. The wires are green and black
and orange. The green and black wires run over to the coil. The orange wire
ties into the other orange wire found in Step W-3 above! The fourth wire on the
duraspark side of the plug (previously not being used) is purple. This purple (previously unused wire) will need to be patched into a new purple wire (included with the Howell kit) and will tie over to the purple wire that plugged into the distributor. Note these are the only wires that need to remain! |
![]() |
Step W-6 The remaining harness (except for the
wires noted in Step W-5 above) can be removed from the engine bay. In doing so, you
need to remove the various parts attached to this wiring harness like the diagnostic plugs
from the side of the battery tray (see second photo), and unplug the harness from various
parts along the harness. The far end of this harness will be over above the manifolds, heading toward the Ignition control module. |
Step W-7 | Now that the excess wiring is removed from the area, patch the wiring from the duraspark over to the coil and distributor. |
![]() |
Step W-8 Set the new wiring harness into the engine bay in its general location, and note the two relays that need to be mounted to the firewall. By mounting the two relays to the firewall, this will sort of act as a place holder for the new harness. The new wiring done in Step W-7 can be stuffed into the new harness, or along side it, as needed. |
![]() |
Step W-9 Feed the new computer wiring plugs through
the access hole in the firewall, and use the rubber bracket (removed in Step W-2) to seal
the new wiring harness to the firewall. Note: Don't fully attach the bracket just yet as another wire (from the next step) will need to pass through this spot! |
Step W-10 | There is an important power wire that needs to be found. Locate a
12V source that has current when the ignition key is in BOTH THE CRANK AND RUN
position. A weatherback connector is supplied for mating this 12V source wire into
the plug at the wiring harness. Attach this wire into the plug. Plug the new
wiring harness (two plugs) into the new ECM. Hint: When searching for a 12V wire, you will have to reconnect the negative battery cable back onto the battery. After doing so, disconnect the rubber cap on the starter solenoid marked with an "S" that feeds the starter. With the starter disconnected, you can now switch the key to the ON and START positions to look for the wire without cranking over the motor. Once you've found your wire, don't forget to re-install the rubber cap and disconnect the negative cable again! |
![]() |
Step W-11 The new computer can be installed. Since the new ECM is longer (as shown in the photo in Step W-1) the old mounting screw will not be used. The back of the new ECM will fit (with a little persuasion) into the old ECM holding bracket. The new ECM can then be attached to the top of the heater duct assembly. Hint: We found that a strip of Velcro tape (two-inch wide by approximately 10-12" in length) with a removable sticky-back worked really well for mounting the ECM to the top of the heater duct surface. |
![]() |
Step W-12 With some of the remaining short pieces of the Velcro tape in Step W-11, mount the new fuse block and diagnostic port to the heater duct assembly. |
Step W-13 | Mount your new Check Engine Light to the dash somewhere, and wire it over to the new fuse block and diagnostic port. The kit does not include the light, so one needs to be purchased. Check either a Radio Shack or an auto parts store for an accessory light. This light will be used to transmit error codes and signify any problems in the system when/if they occur. Re-install the glove box insert. |
ASSEMBLY | |
![]() |
Step A-1 The new fuel pump and fuel filter can now
be attached together. Remember, the fuel filter connects BEFORE the fuel pump in the
system, so the fuel (from the tank) will pass the filter before entering the electric
pump. Tip! Before installing the pump, check to make sure the brass fitting on the output (forward) side of the pump is tight, or it will leak when the motor is running. |
Step A-2 | The fuel pump/filter assembly will mount using two of the existing fuel hard line mount bracket bolt holes above the transfer case crossmember/skidplate. As such, the fuel hard line needs to be cut back a short distance behind the second mount bracket. When cutting the hard line MAKE SURE YOU HAVE A PLUG FOR THE FUEL LINE! (It also may help not to start this project with a FULL fuel tank!) We found the small red protective cap for the new fuel pump worked well for this! Cut the line with a small tubing cutter. |
![]() |
Step A-3 With the hard line cut, and the fuel pump/filter assembled, install fuel pump assembly on the inside of the passenger side frame rail above the transfer case crossmember/skidplate. A strap is provided for the fuel pump, and you can use the bolt hole (and bolt) from the old hard line mount. About a foot of fuel line will connect the hard line to the fuel filter. The remaining fuel line provided in the kit is attached to the front of the pump and will run up to the firewall, around the back of the motor, and to the TBI unit. |
![]() |
Step A-4 Locate the adapter plate for the TBI unit
and the provided gasket. We noticed here that the gasket provided for mounting the adapter plate to the intake manifold left little to be desired. This gasket was hand-cut with four holes punched through it for the mounting bolts. Unfortunately, the punched holes didn't come close to aligning with the four drilled holes on the adapter plate! As it so happened, I had a few unused base gaskets left over from an old Carter BBD rebuild kit laying around. So we used one of the new gaskets since it looked and fit much nicer than the provided gasket. |
![]() |
Step A-5 Find the four new allen bolts provided
with the adapter plate. Mount the gasket and adapter plate to the top of the intake
manifold and install with the four new bolts. The second photo shows the new gasket used to mate the TBI unit to the adapter plate. If you look were the two fingers are pointing in this photo, you'll notice the tops of two of the allen bolts are visible. You can also see the tops of the two other allen bolts visible in the taper cut in the adapter plate. These will be a source of vacuum leaks and need to be sealed. Once the bolts are tightened sufficiently, apply silicon to the tops of all four allen bolts. Make sure to fill all recesses slightly above the surface of the adapter plate, you'll want this to form an air-tight seal. Be thorough, and be neat! You will want to coordinate this step soon enough into the install process to allow the silicon to set up for a few hours. The instructions recommend at least four hours. We applied this late one evening and let it set-up overnight. |
![]() |
Step A-6 Mount the new gasket (shown in second photo above in Step A-5) and TBI unit atop the adapter plate. The TBI unit is held onto the adapter plate with bolts provided in the kit. |
![]() |
Step A-7 The kit provides two lengths of fuel line. The narrower diameter hose is for the fuel return line. Attach one end of the smaller hose to the fuel return hard line, located on the driver's side frame rail on the CJs. |
![]() |
Step A-8 The instructions provide a very clear
vacuum line routing diagram and the vacuum ports on the TBI unit are all labeled with a
letter code (see top photo). Connect the vacuum lines with the TBI unit. Basically, the PCV valve line connects to the top port and it's T'd with the large line running down to the charcoal vapor canister. The port below has another T that ties the vacuum advance line over to the distributor with the two Y'd lines at the CTO valve. The EGR valve is also connected to a third port at the CTO valve. The fourth port on the CTO (purge control) is connected to the charcoal vapor canister. Pretty simple! |
Step A-9 | If you haven't done so yet, install the new O2 sensor into the exhaust header pipe. |
Step A-10 | Connect the throttle linkage to the TBI unit. The linkage rod (removed from the Carter BBD) just clips onto the pin on the TBI linkage. No springs are needed as the TBI already has a spring built onto its linkage. |
Step A-11 | The fuel return and fuel main hoses can be attached to the TBI unit at this time. |
![]() |
Step A-12 The new Manifold Absolute Pressure (MAP) sensor can now be mounted. This has to be located somewhere ABOVE the TBI base plate location - very important! I attached this one to the main wiring harness near the brake master cylinder. The vacuum line is connected to a port located between the fuel return and main lines on the rear of the TBI unit. |
Step A-13 | Connect the wiring harness to the firewall and route the fittings, connecting them to the sensors and TBI unit. Route the remaining portion of the harness down toward the fuel pump and transmission (on the passenger side of the motor). |
Detour | Here is where we installed new heater hoses on our project! With the new Coolant Temperature sensor installed (if you didn't do so already in Step D-9) you can now top off the coolant in the system. |
![]() |
Step A-14 Install the new Speed Sensor. This unit attaches to the end of the speedometer cable before it enters into the transfer case. Just unscrew the cable from the transfer case and insert the cable onto the threaded end of the Speed Sensor. Now, bolt the Speed Sensor back into the transfer case. Plug the wire into the end of the wiring harness. |
Step A-15 | Attach the remaining wire from the harness to the fuel pump. There may be some excess wire. We ran the excess length back up under the battery and attached the looped excess to the firewall up out of the way to prevent it from being snagged on anything later. |
![]() |
Step A-16 Attach the air cleaner element to the top of the TBI. The Howell kit includes the off-set mounting bolt (for the top of the air cleaner lid) and a new rubber gasket for the base of the air cleaner and top of the TBI unit. You will need to run the breather hose from the back of the valve cover into the base of the air cleaner tray. |
![]() |
Step A-17 Attach the provided label decal to the front grill top (where the old vacuum diagram decal was located). This is important, as it provides the vacuum routing information. |
Step A-18 | Did you remember to cap the two air tubes from where the old Pulse Air system was removed? This step may require welding. |
Step A-19 | Double-check that all the lines and wires are properly connected and attached safely. Use lots of zip-ties to secure the wires from contacting hot parts or moving parts! Reconnect the negative cable back to the battery. |
Step A-20 | Start it up! At first, turn the key on and listen for the fuel pump to run for a few seconds, it will run stop automatically. Turn to key to start and it WILL have to crank over several times (don't worry) and a few sequences. You will most likely have to crank it a few times as the fuel lines purge all the air through the system. You will probably hear them hiss, just before the engine fires! Check immediately for fuel leaks!!! |
Results?
The main reason for installing this fuel injection kit onto this Jeep was to resolve the cool weather stalling/poor idle problem. Two weeks after we finished installing the kit, we were still having problems with poor cold-engine stalling. At first, we suspected it had to do with the old emissions parts still in the system and went through and performed checks on each device to see if that changed anything, and it didn't. We believe the problem has to do with a change in voltage going to the ECM. We hooked the Jeep up to a diagnostic scope and it indicated a significant voltage change between the battery and the switched-power source to the ECM. So a new power source needed to be found.
As for increases in gas mileage, so far the Howell has resulted in an increase of 2 - 3 MPG on the freeway. The Howell, on occasion, has had some pinging problems due to hot weather/high street asphalt temperatures.